Four boreholes in beautiful Tuscany
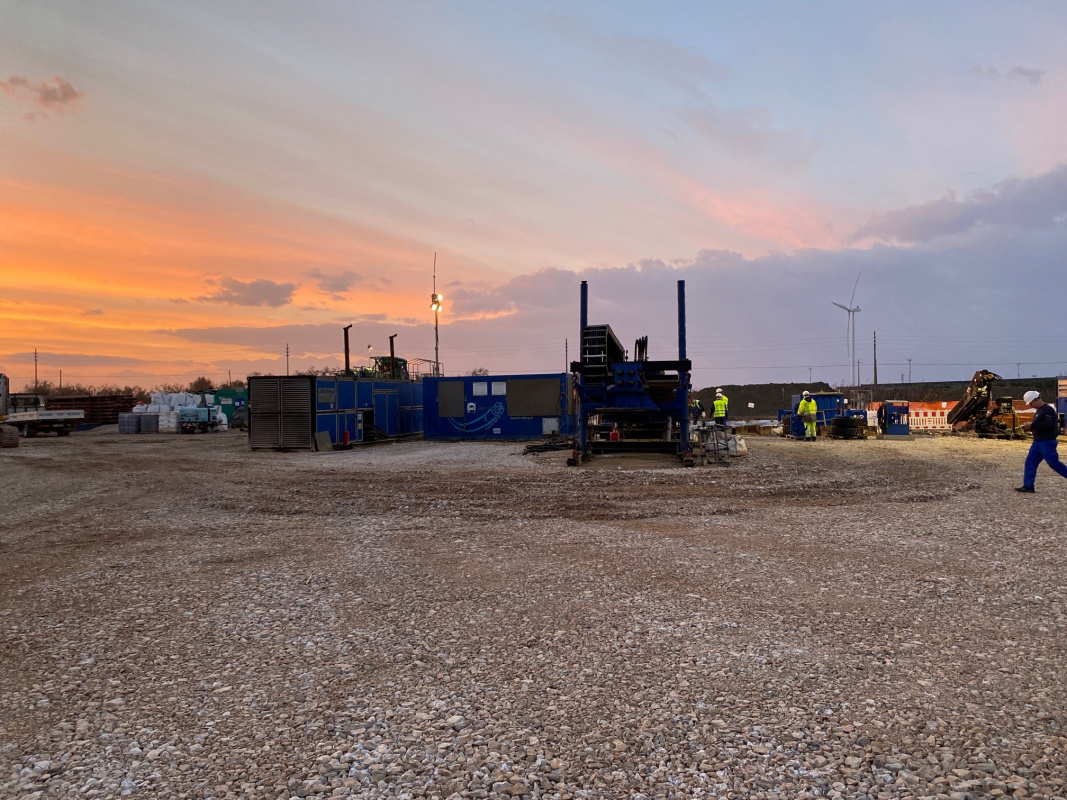

Like most European countries, Italy is experiencing gas supply problems as a result of the war in Ukraine. That is why an LNG terminal is being built in Piombino (Tuscany), which is scheduled to be operational in March 2023. In order to connect this terminal to the Italian gas network, it is necessary to build a pipeline of about 8.8 km in total on behalf of SNAM RETE GAS SPA (SRG), consisting partly of a single 48” pipeline and partly of two 26” pipelines. Parallel to the gas pipeline, a 6” cable conduit for a fibre optic cable is laid.
At the end of November 2022, LMR signed the contract with the Main Contractor, Max Streicher SpA (Italy), for the crossing of the Cornia River, which was to be crossed with three boreholes (1 × 6” cable conduit and 2 × 26” gas pipeline) of 550 m each. Work preparation began immediately, and at the beginning of December the first trucks were already heading to Italy.
By December 16th, all the equipment was set up and drilling for the 6” casing could begin, as this had to be completed before Christmas. Despite less-than-ideal working conditions, linguistic and cultural differences between Italy and Germany, which occasionally caused confusion and misunderstandings, and partly deviations from the subsoil investigations, the pipe was successfully installed on December 19th. The team travelled home for their well-deserved Christmas vacation and returned on January 2nd, 2023.
Due to the time pressure in the overall plan, the next two 26” crossings for the gas pipeline had to be carried out in 24/7. Over time, cooperation with the client continued to strengthen, and the two crossings were executed without any problems. The second gas pipeline was even finished two days earlier than planned.
During our work, SRG and Max Streicher SPA carried out various safety and environmental checks, which were completed without any problems.
Both the customer and our client were very satisfied with LMR’s performance, and shortly before demobilisation, we received another order: Parallel to a 48” direct pipe to be carried out by a third party in January/February 2023, LMR was to drill a 1,250 m long hole for the 6” cable conduit in March 2023.
The equipment was stored in a safe area of the port of Piombino, and the crew travelled back to Germany.
The entry point of the new crossing was located on part of a newly constructed section in Piombino’s port area, next to the new landing stage of the LNG ships. This dam was an artificial structure built from large rocks, stones and sand, which is not a suitable soil for HDD. Therefore, during our absence, another contractor installed a 20” casing pipe with a length of 80 m from the surface to the original seabed.
As soon as the direct pipe was completed, LMR mobilised the first part of the crew and began setting up the HDD equipment. Rarely, our workspace is so beautiful and level. The entire surface was covered with a fresh layer of asphalt, which the client had to cut in for our entry pit, pump sumps and grounding systems. To avoid further damaging of the surface, dams were built from sandbags to prevent drilling fluid from flowing over the site.
It was not so easy to arrange the transport. Our project was located in a new port as well as in an old steel mill that was dismantled during our construction work. There was a guarded gate at the entrance to the site, and to be allowed to pass through it, the license plates of all cars and trucks, as well as the names of all employees and drivers, had to be submitted in good time before arrival. This procedure turned out to be extremely nerve-wracking because transport companies often decide at the last minute which trucks to use. However, with the help of our local representative, our site managers managed to bring the trucks and two cranes to the site and set up the equipment, so drilling work could be started on the night shift.
Due to the available soil information as well as the experience with the river crossing (the exit points of the two boreholes are less than a kilometre apart) and the length of the borehole, we decided to use a so-called drilling motor. This is a system that requires less contact pressure on the chisel because it is driven (rotated) by the mud while the drill string is rigid. This drill motor, unlike the Jetting Assembly, is heavier and longer. When it became apparent that the ground was too soft for such a system for the first 150 m, the drill motor was removed from the borehole and the borehole was continued with a jetting assembly. This went well until, after 700 m, the mud return flow from the borehole stopped. This was a serious challenge, as the fresh water supply was a huge problem in the port area as well as the previous construction site. Although our main client was anxious to organise sufficient quantities of water to be transported by water trucks to the port area and stored there temporarily, it was inevitable that there would be occasional shutdowns.
In the last 200 m we encountered hard spots again, as we have done occasionally on the entire borehole. These spots took up a lot of drilling time and therefore a lot of drilling fluid. The water supply became very critical, especially at night, as there was a driving ban for trucks, which led to temporary stoppages on the night shift. However, just before the punch out, the ground softened again, and we managed to finish the pilot bore with the remaining water. After finishing the drilling around 10.00 p.m., the jetting assembly on the pipesite was dismantled and the 6” cable conduit was connected to the drill string. Shortly after midnight, the pipe installation could begin. Including four warranty welds, the pull-in process for the 1,250 m was completed in just 13 hours.
All that remained was the demobilisation of the construction site as well as the cleaning and loading of the equipment. The customer was very satisfied with the fast and safe work, but was even happier when the site area was free of LMR equipment and was able to start his planned work on the construction site.
Jorn Stoelinga, LMR
all news